
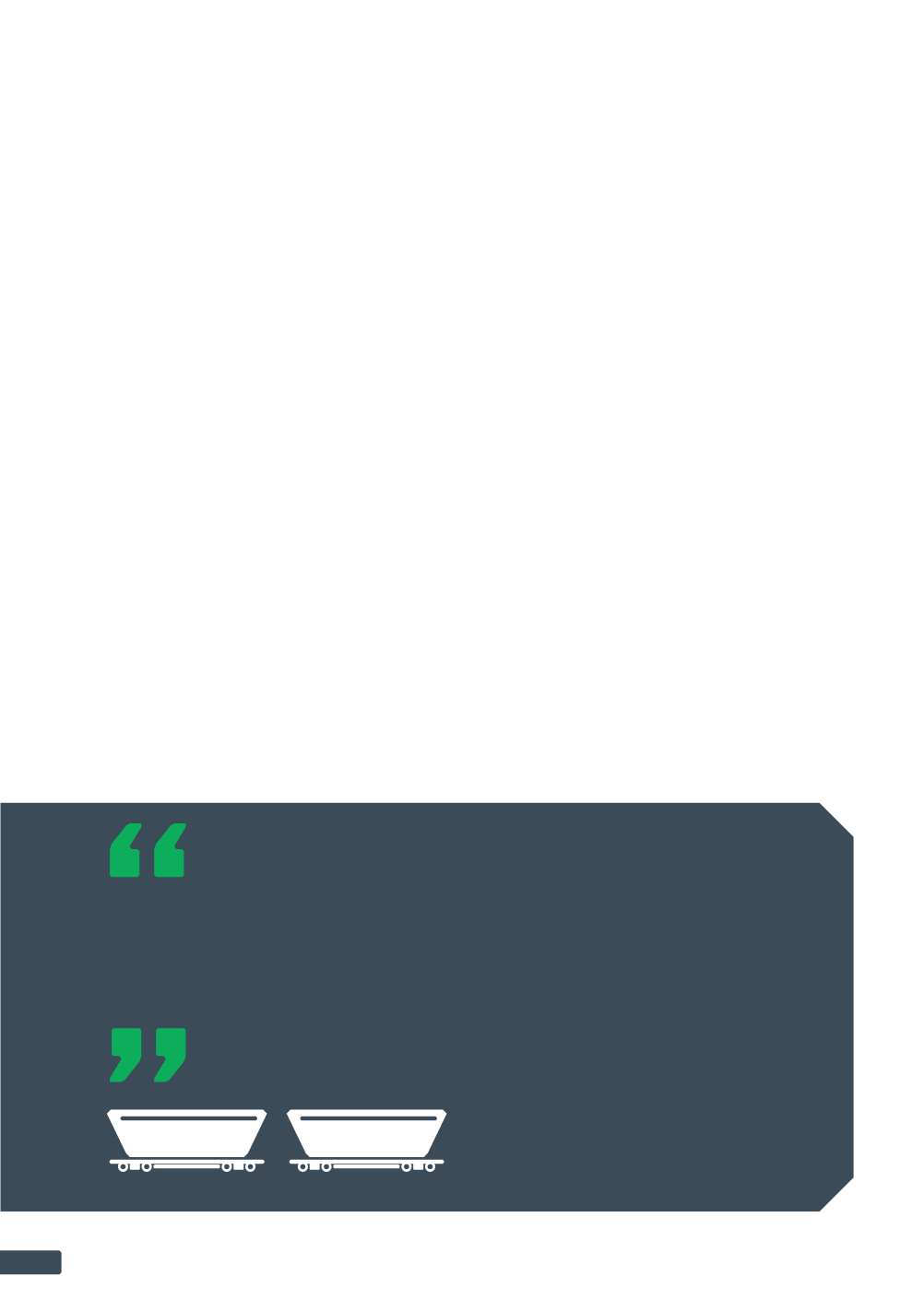
in better overall infrastructure reliability
once the entire network was restored.
The January flooding brought over
200mm of rain that resulted in localised
flooding and closure of a section of track
between Sandgate and Warabrook, halting
passenger, coal and freight services.
•
•
We’ve partnered with our customers to
progress the development of a business
case for ANCO (ARTC Network Control
Optimisation). This project aims to provide
our Network Controllers with advanced
tools and more reliable data to enable
faster, more informed decisions to better
manage train flow and all other activities
on track, helping to deliver the right trains
at the right time. Our focus is on improving
the customer experience through increased
operating efficiency, asset availability and
reliability, as well as provide the opportunity
to grow our services, particularly in the
non-coal area.
•
•
We consulted with customers and supply
chain members to improve the way we
schedule our track maintenance work.
Moving from four planned track
possessions a year to six reduced the
need for smaller subsequent possessions,
providing more certainty and enabling coal
customers to transport more coal to port.
•
•
We’ve run successful trials staging loaded
trains on the network in lower utilised
areas resulting in more efficient running
of trains in the busier sections.
•
•
We have significantly improved
performance reporting for our customers.
The reporting covers operational efficiency,
asset management efficiency and overall
supply chain efficiency and highlights
areas for improvement on a daily and
weekly platform. It will assist in targeting
improvements in performance and growth
opportunities by area and enable more
efficient use of our assets.
•
•
Across our Provisioning Centres
we’ve been implementing a continuous
improvement program, engaging our
leaders and their teams to improve
operating disciplines, generate improvement
ideas and make changes about how their
work is performed. These initiatives have
included improved maintenance planning
tools, defect management, improved daily
planning and new meeting structures.
We have focused on supporting our
leaders so we can embed a cohesive
and sustainable approach.
WE DOUBLED
THE PAYLOAD
OF A STANDARD
GRAIN TRAIN
We doubled the payload of a standard grain
train – saving growers dollars and providing
a basis on which to make grain transport
more efficient. In December history was
made when the largest, continuously-
tipped export grain train in Australia
departed NSW’s north west for the Port
of Newcastle. This 1,300 metre train’s
capacity of more than 5,000 tonnes more
than doubled the payload of a standard grain
train that runs through the Hunter Valley
network and the increased payload resulted
in cost savings for the grower. Making the
move to larger and heavier trains also builds
efficiencies into the supply chain and we
are continuing to work with grain producers
to enable this into the future.
18